Email: katrina@qidumetro.com Phone: (+86) 134 1323 8643
How to Use Touch Probes for Increased Efficiency and Cost Savings
The integration of touch probes into cnc machine tool workflows can significantly improve both processing efficiency and accuracy, ultimately leading to cost savings. This article delves into the effective utilization of touch probes, encompassing probe selection, installation, calibration, and usage techniques.
1. Selecting the Right CNC Touch Probes
A diverse range of CNC probes exists, necessitating careful selection based on specific factors like workpiece size, shape, required precision, and machine tool capabilities.
Classification by Measurement Method:
CNC probes fall into two primary categories: contact and non-contact. Contact probes physically touch the workpiece surface for measurement, while non-contact probes utilize methods like optical, electromagnetic, or other non-physical approaches.
Classification by Measurement Accuracy:
CNC probes can be further classified as precision probes and standard probes. Precision probes deliver high measurement accuracy, catering to applications demanding high-precision machining, while standard probes offer lower accuracy, suitable for general machining tasks.
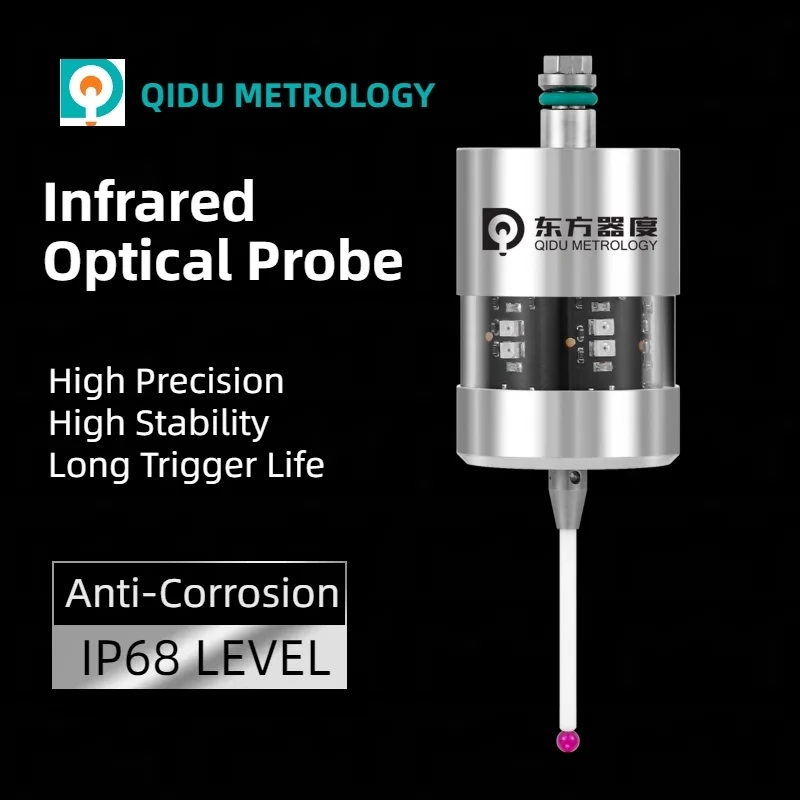
2. Installing the CNC Probe
CNC probe installation necessitates adherence to the following key points:
Mounting: The probe needs to be securely mounted on the machine tool spindle or tool changer, ensuring proper alignment with the machine’s coordinate system.
Positioning: The distance between the probe and the workpiece surface must be appropriate for accurate tool measurement.
Security: The installation should ensure the probe remains firmly in place throughout the measurement process, preventing any loosening.
3. Calibrating the CNC Probe
Calibration is essential for ensuring measurement accuracy prior to utilizing the touch probe. Common calibration methods include:
Standard Ball Calibration: A standard ball is mounted on the machine tool, and its diameter is measured with the probe. The obtained value is compared to the known standard value to determine any probe error.
Laser Interferometer Calibration: This method utilizes a laser interferometer to measure the three-dimensional position of the probe, with the obtained value compared to a standard value to identify any probe error.
4. Effective CNC Probe Usage Techniques
During the measurement process:
Maintaining a clean workpiece surface: This is crucial to prevent contamination of the probe, ensuring accurate readings.
Regular maintenance: Regular maintenance and servicing are essential for maintaining the probe’s accuracy and optimal functionality.
Selecting the appropriate measurement program: Choosing the correct program based on the workpiece characteristics is vital for accurate and efficient measurements.
5. Advantages of Utilizing CNC Probes
The effective use of touch probes offers several compelling benefits:
Enhanced Processing Efficiency: CNC probes automate workpiece dimension measurement, significantly reducing time and minimizing errors associated with manual measurement.
Improved Processing Accuracy: By eliminating reliance on manual procedures, touch probes promote consistent and accurate measurements, leading to superior processing quality.
Reduced Production Costs: Increased processing efficiency and accuracy translate to reduced material waste and rework rates, ultimately lowering production costs.
Conclusion:
CNC probes play a vital role as auxiliary tools in CNC machine tool operations. Their effective selection, installation, calibration, and usage can significantly elevate processing efficiency and accuracy, leading to substantial cost savings. By actively implementing best practices for CNC probe utilization, companies can unlock their full potential and optimize CNC machine tool operations.