Email: katrina@qidumetro.com Phone: (+86) 134 1323 8643
Probe for CNC machine are crucial for ensuring precise measurements in manufacturing. However, system errors can impact their accuracy. This article explores five common types of machine tool probe system errors and how to minimize them.
Types of System Errors of Probe for CNC machine
1.Static Errors:
These arise from the probe’s physical properties and settings. They include:
- Dead Zone Error:Bending of the probe’s stylus upon contact with the workpiece creates a slight measurement inaccuracy.
- Repeated Positioning Error:While less frequent, this error occurs due to slight variations in the probe’s positioning during repeated measurements.
Minimizing static errors often involves optimizing contact pressure settings and using a probe with a stiffer stylus or shorter length.
2. Dynamic Errors:
These stem from the interaction of the probe with the CNC system. They are caused by:
- Probe Contact Speed:An excessively fast or slow probe contact speed can lead to inaccurate measurements.
- Sampling Interval:The CNC system’s sampling frequency for probe signals can affect accuracy.
Optimizing these errors usually involves setting the ideal probe contact speed and sampling interval within the CNC system’s settings.
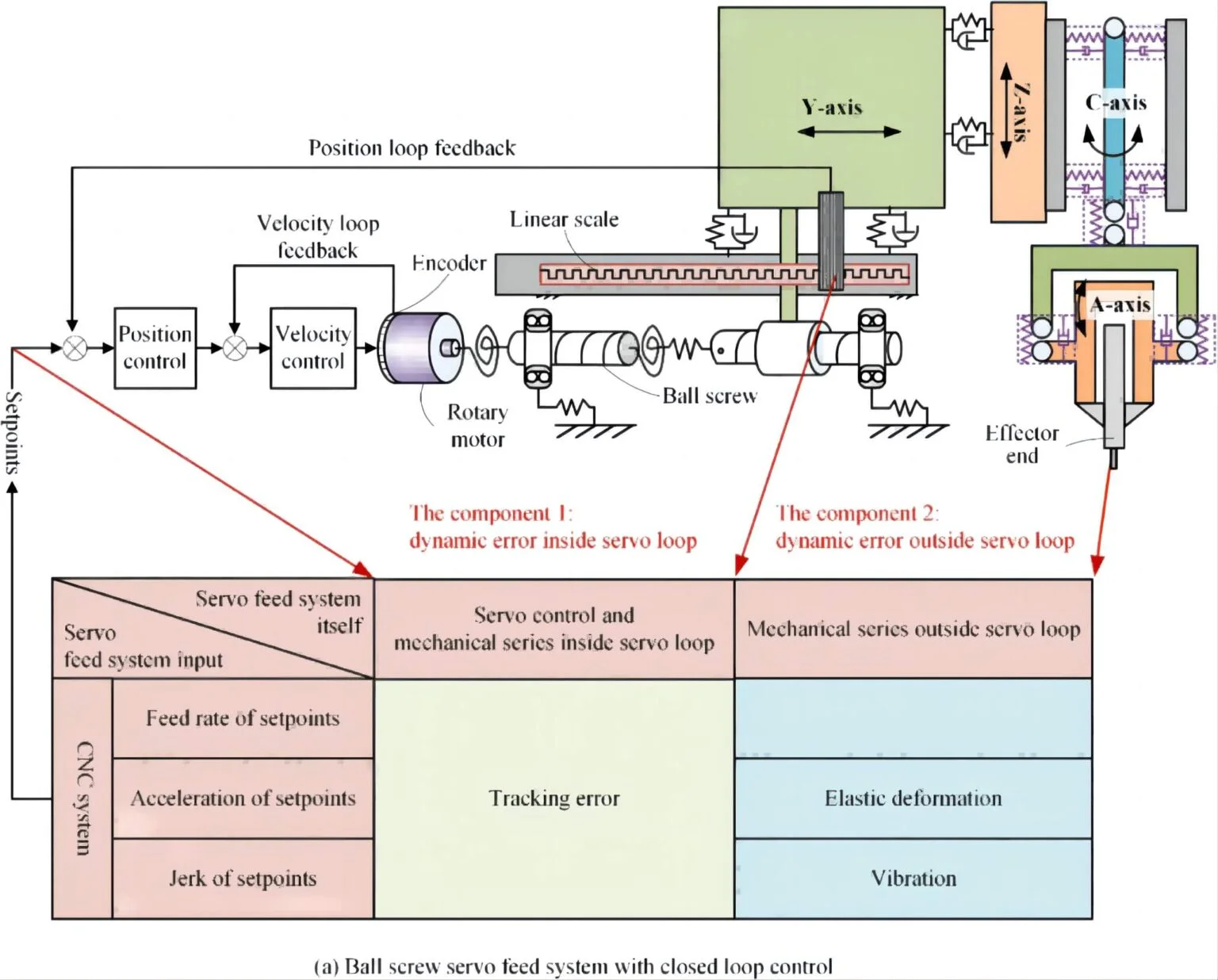
3.Installation Errors:
These errors occur due to mistakes during probe installation and can be caused by:
- Software Issues:Incorrect probe configuration within the CNC software.
- Hardware Issues:Improper physical mounting of the probe on the machine tool.
Thorough adherence to the manufacturer’s installation instructions and proper training for machine operators can significantly reduce installation errors.
4.Thermal Errors:
Fluctuations in temperature can cause the probe’s components to expand or contract, leading to measurement inaccuracies. This can be caused by:
- Ambient Temperature Changes:Variations in shop temperature can affect the probe’s performance.
- Heat Generated by the Machine:Heat generated by the machine tool itself can also impact probe accuracy.
Maintaining a controlled shop temperature and using probes designed for thermal stability can help mitigate these errors.
5. Electrical Noise:
Interference from electrical signals within the machine tool environment can disrupt the probe’s signal transmission, causing false triggering or inaccurate measurements. This can be caused by:
- Faulty Grounding:Improper grounding of the machine tool or probe can lead to electrical noise.
- Nearby Equipment:Other electrical equipment in the vicinity might generate interference.
Ensuring proper grounding practices and minimizing the presence of noisy equipment near the machine tool can help reduce electrical noise errors.
By understanding these common system errors and implementing appropriate solutions, manufacturing companies and machine tool operators can ensure their probes deliver highly accurate measurements, leading to improved quality control and production efficiency.

Katrina
제조 업계에서 10년 이상의 경험을 보유한 기계 영업 엔지니어. 영업 전략 개발 및 실행, 고객과의 관계 구축 및 거래 성사에 능숙합니다. CRM 소프트웨어, 리드 생성 도구, 소셜 미디어를 포함한 다양한 영업 및 마케팅 도구에 능숙합니다. 나는 판매 목표와 목표를 달성하기 위해 독립적으로 그리고 팀의 일원으로 일할 수 있습니다. 지속적인 개선과 새로운 판매 기술 학습에 전념합니다.