Email: katrina@qidumetro.com Phone: (+86) 134 1323 8643
Setting up a tool setter installation on your CNC machine can significantly enhance your precision and efficiency in machining operations. Below, we provide a step-by-step guide to ensure a smooth and secure installation process.
Step 1: Securing the Tool Setter Base
Preparing the Setter Alat: Upon unboxing the product, use a clean cloth to thoroughly wipe the base. This removes any dust or particles that could interfere with a secure installation.
Mounting the Base: Locate the provided screws in the packaging. Firmly attach the setter to the designated area on your CNC machine. Tighten the screws securely to prevent any movement or instability during machine operation. This is crucial to maintaining the accuracy and reliability of the tool setter.
Connecting the Cables: Identify the corresponding ports on your machine control console. Connect its cables to these ports, ensuring a snug fit. This connection is vital for integrating the tool setter into the machine’s control system and for it to function correctly.
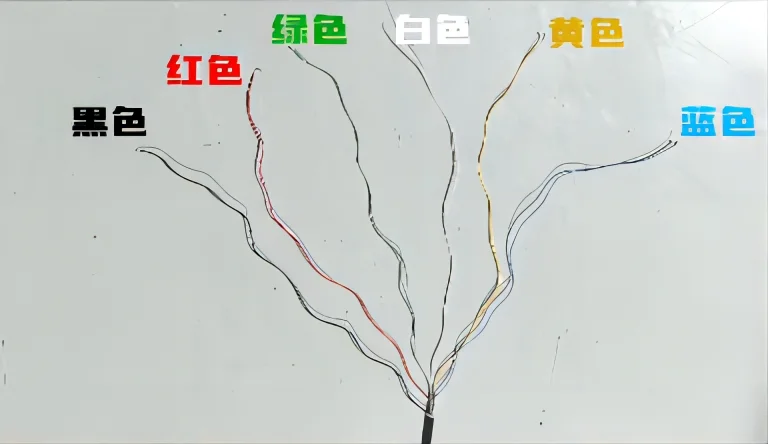
Step 2: Integrating the Tool Setter with the Machine’s Electrical Circuit
Ensuring Safety: Before beginning any electrical work, ensure that the machine’s power is completely turned off. This safety measure prevents any potential electrical faults or accidents during the installation.
Loosening Screws: Use an appropriate screwdriver to loosen the screws at the back of the machine. This step prepares the machine for the upcoming wiring tasks and provides access to the internal components.
Connecting to the KIP Interface: Find the KIP interface on your CNC machine. Correctly insert the Mitsubishi connector into this interface. The KIP interface is a standard connection point for integrating additional equipment into the machine’s control system.
Power Line Connections: Connect the its red and black wires together first. Then, attach them to the machine’s main power supply. These connections are crucial for powering the tool setter and ensuring it operates in sync with the machine.
White Wire Connection: Ensure that the white wire from the Mitsubishi connector and the white wire from the tool setter are properly connected to the machine’s power source. This connection facilitates communication between the tool setter and the machine’s control system.
Restoring the Circuit: Carefully reinsert the machine’s circuit components that were removed or loosened earlier. Verify that all connections are correct and securely in place to avoid any disruptions in the machine’s operations.
Connecting Green and Blue Wires: Attach the blue wire from the Mitsubishi connector to the green wire of the tool setter. This link is essential for establishing a proper electrical connection that supports the tool setter’s functions.
Emergency Stop Safety Integration: Loosen the emergency stop protection circuit and connect the tool setter’s yellow wire to it. Next, link the original emergency stop wire to the tool setter’s blue wire. This integration ensures that the tool setter can respond appropriately in an emergency stop situation.
Securing All Screws: After completing all wiring, re-tighten all previously loosened screws. Ensure all connections are stable and there is no looseness, which could lead to operational issues or safety hazards.
Kesimpulan
Proper installation of a tool setter is fundamental for achieving high-precision and efficient operations in CNC machining. By following these detailed steps, you can ensure that your setter is securely mounted and correctly integrated into your machine’s electrical system. This meticulous process not only safeguards your equipment but also maximizes the performance and longevity of your machining operations.
For an effective and smooth operation, always adhere to these installation guidelines. Your machine’s reliability and precision are only as strong as the care you put into its setup.
FAQ of Tool Setter Installation
Q1: Why is it important to clean the base of the tool setter before installation?
- A1: Cleaning the base ensures that no debris interferes with the stability of the setter, which is crucial for maintaining precision during machining operations.
Q2: How can I ensure that the tool setter is securely mounted?
- A2: Make sure to use all provided screws and tighten them firmly. Check for any movement by gently applying pressure to the tool setter. It should remain stable without any wobbles.
Q3: What should I do if the tool setter’s cables don’t fit the machine’s ports?
- A3: Double-check the machine’s control console ports to ensure you are using the correct ones. If the problem persists, consult the its manual or contact the manufacturer for assistance.
Q4: Why is it necessary to connect the tool setter to the KIP interface?
- A4: The KIP interface is a standard connection point that allows the setter to integrate with the machine’s control system, enabling it to communicate and function correctly with the CNC machine.
Q5: How do I know if all the electrical connections are correct?
- A5: Follow the wiring diagram provided by the produsen penyetel alat. After connecting, double-check each wire to ensure it is securely fastened and corresponds to the correct terminal.
Q6: What is the role of the emergency stop integration?
- A6: Integrating it with the emergency stop system ensures that it will halt operations in case of an emergency, providing an additional layer of safety during machine operation.
Q7: What should I do if the tool setter still moves after installation?
- A7: Recheck all mounting screws and tighten them if necessary. Verify that the base is clean and properly aligned. If the problem continues, inspect the machine surface for any irregularities that might affect stability.
Q8: Can I install the tool setter without turning off the machine’s power?
- A8: No, always ensure the machine’s power is completely off before starting the installation. Working with live electrical circuits can be hazardous and may damage the equipment.

Katrina
Mechanical Sales Engineer with 10+ years of experience in the manufacturing industry.Skilled in developing and executing sales strategies, building relationships with customers, and closing deals. Proficient in a variety of sales and marketing tools, including CRM software, lead generation tools, and social media. I'm able to work independently and as part of a team to meet sales goals and objectives. Dedicated to continuous improvement and learning new sales techniques.