Email: katrina@qidumetro.com Phone: (+86) 134 1323 8643
What is a Probe for CNC & How to Use It?
In the world of CNC machining, precision and accuracy are paramount. Even the slightest deviation from the programmed path can result in flawed parts and wasted materials. This is where probe for CNC come in – indispensable tools that elevate CNC machining to a whole new level of efficiency and control.
Importance of Probe for CNC
Probes act as the sensory organs of a CNC machine. They provide valuable real-time data on the position and characteristics of the workpiece, enabling the machine to adapt and adjust its movements for exceptional results. Here’s how probes contribute to successful CNC machining:
- Lyhennetyt asennusajat:Manually setting tool offsets and workpiece zero points can be time-consuming. Probes automate this process, significantly reducing setup times and increasing overall machine utilization.
- Parempi osien laatu:By verifying tool lengths and workpiece positions before machining begins, probes minimize errors and ensure consistent part quality throughout production runs.
- Minimoitu materiaalihävikki:With precise tool offsets and workpiece identification, probes prevent accidental tool-workpiece collisions, saving valuable material and reducing scrap rates.
- Enhanced Process Automation:Probes enable automated in-process inspection, allowing the CNC machine to identify potential issues and adjust parameters for uninterrupted machining.
Understanding the Basics of a Probe for CNC
There’s more to probes than meets the eye. Let’s delve deeper into their functionalities and different types:
1. What is a Probe for CNC?
A probe for CNC is a specialized tool that attaches to the spindle or tool changer of a CNC machine. It typically consists of a body, a spring-loaded stylus, and a triggering mechanism. The stylus makes contact with the workpiece surface, sending a signal to the CNC control unit which interprets the data for various applications.
2. Types of Probe for CNC
Probes come in various configurations, each suited for specific applications. Here are the two main categories:
- Contact Probes:These are the most common type. Contact probes utilize a spring-loaded stylus that triggers a signal upon contact with the workpiece. They are ideal for tool offset setting, workpiece zeroing, and basic in-process inspection.
- Non-Contact Probes:These probes employ technologies like lasers or vision systems to gather data without physically touching the workpiece. Non-contact probes are well-suited for delicate surfaces or applications requiring highly precise measurements.
Within these categories, probes further differentiate based on their triggering mechanisms and functionalities. Some common types include:
- Touch Probes:The workhorse of probe for CNC, these utilize a mechanical switch triggered by stylus contact with the workpiece.
- Analog Probes:These probes provide continuous force data, enabling measurement of surface variations and contouring.
- Radio Frequency Identification (RFID) Probes:These probes contain an embedded chip that transmits identification data to the CNC control unit, facilitating automated tool and workpiece recognition.
The Importance of Using Probes in CNC Machining
Probes offer a multitude of benefits for CNC machining, making them a valuable investment for any workshop. Here are some key advantages:
1. Enhancing Precision and Accuracy
By automating tool offset setting and workpiece zeroing, probes eliminate human error and ensure consistent machining accuracy. This is particularly crucial for complex geometries and tight tolerance applications.
2. Improving Efficiency
Probes significantly reduce setup times by automating critical tasks. Additionally, probes enable unattended machining with in-process inspection capabilities, minimizing the need for operator intervention.
3. Quality Control
Probes facilitate continuous part inspection throughout the machining process. This allows for early detection of potential issues and corrective actions to be taken, preventing production of defective parts.
How to Use a Probe for CNC
While specific procedures may vary depending on the CNC machine and probe model, the general process of using a probe for CNC machining involves the following steps:
1. Setting Up Your Probe
- Probe Installation:Mount the probe for CNC onto the spindle or tool changer according to the manufacturer’s instructions.
- Probe Calibration:Calibrate the probe to ensure accurate measurements. This typically involves setting a reference point and measuring a known distance.
- Probe Configuration:Configure the CNC control unit to recognize and communicate with the probe. This may involve selecting the probe type, defining probe offsets, and setting probe parameters.
2. Programming the Probe
- Probe Programming:Incorporate probe commands into the CNC program. These commands define the probing points, desired actions, and any relevant parameters.
- Probe Cycle Programming:Create a probe cycle that outlines the sequence of movements, probe activations, and data interpretation for each probing task.
- Probe Integration:Integrate the probe cycle into the overall CNC program, ensuring seamless execution of probing operations alongside machining tasks.
3. Conducting Measurements and Inspections
- Työkalun offset-asetus:Use the probe to establish accurate tool offsets by touching the probe stylus to the tool tip and referencing it to a known point on the workpiece.
- Workpiece Zeroing:Set the workpiece zero point by probing a reference point on the workpiece surface and defining it as the origin for subsequent machining operations.
- In-Process Inspection:Utilize the probe to inspect workpiece features, dimensions, and surface conditions during machining, enabling real-time quality control.
4. Troubleshooting Common Issues
- Probe Misalignment:Verify probe alignment to ensure accurate measurements. Adjust probe mounting or stylus orientation if necessary.
- Probe Triggering Errors:Check probe calibration, stylus condition, and signal transmission. Clean the stylus and ensure proper connection to the CNC controller.
- Software Communication Issues:Check probe configuration settings and communication protocols. Update CNC software or probe drivers if necessary.
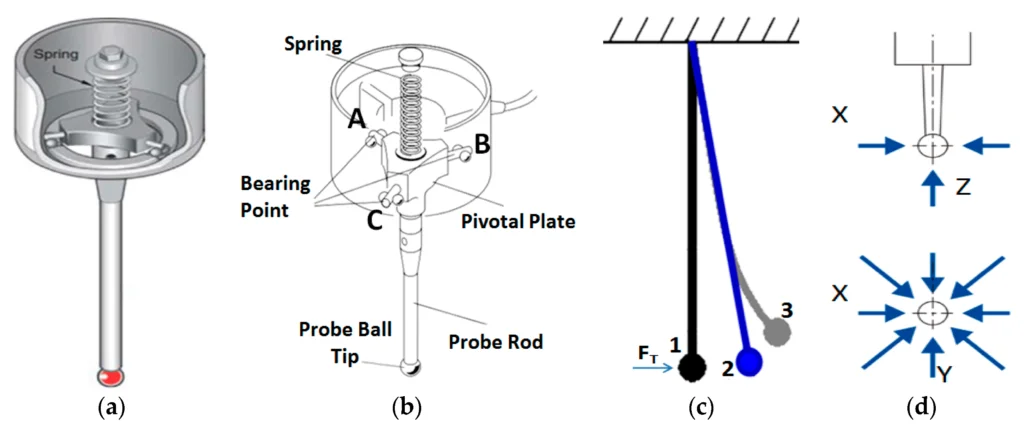
Choosing the Right Probe for CNC in Lathe
Selecting the appropriate probe for your CNC machine depends on several factors:
- Machining Requirements:Consider the types of machining operations, workpiece materials, and desired precision levels.
- Probe Type:Contact probes are suitable for general applications, while non-contact probes offer higher precision and versatility.
- Probe Features:Evaluate probe characteristics like stylus size, triggering mechanism, communication protocol, and compatibility with your CNC machine.
- Budjetti:Probe prices vary depending on features and capabilities. Set a realistic budget and consider the return on investment.
Popular Probe Brands and Models
Several reputable brands offer a wide range of probe for CNC, each with its own strengths and applications. Here are a few examples:
Renishaw:Renishaw is a leading manufacturer of high-precision contact and non-contact probes for various CNC machining applications.
Heidenhain:Heidenhain offers a comprehensive range of probe for CNC, including touch probes, analog probes, and RFID probes, for diverse CNC machining needs.
Blum:Blum specializes in contact probes for tool offset setting, workpiece zeroing, and basic in-process inspection.
Qidu Metrology:Qidu Metrology provides cost-effective contact and non-contact probes for general CNC machining applications.
Johtopäätös
Probes have become indispensable tools in the world of CNC machining, enhancing precision, efficiency, and quality control. Their ability to automate critical tasks, provide real-time data, and enable advanced applications makes them a valuable investment for any workshop. By carefully selecting the right probe and utilizing it effectively, manufacturers can elevate their CNC machining capabilities to new heights.
FAQs about Probe for CNC
1. How do I calibrate a CNC probe?
Probe calibration is crucial for ensuring accurate measurements. The specific calibration procedure varies depending on the probe type and CNC machine. However, the general steps typically involve:
- Establishing a reference point:Define a known reference point on the machine or workpiece that serves as a basis for calibration.
- Measuring a known distance:Use the probe for CNC to touch the reference point and then touch another point at a known distance from the reference.
- Adjusting probe parameters:Based on the measured distance, adjust the probe’s internal parameters to ensure it accurately represents the actual distance.
- Verifying calibration:Repeat the calibration process with different reference points and distances to verify the probe’s consistency.
- Documenting calibration:Record the calibration data and date for future reference and traceability.
2. Can I retrofit a probe to an existing CNC machine?
In most cases, yes, you can retrofit a probe to an existing CNC machine. The feasibility and complexity of the retrofit depend on the machine’s capabilities, available mounting points, and compatibility with the chosen probe. Consult with the CNC machine manufacturer or a qualified technician to assess the suitability of retrofitting a probe to your specific machine.
3. What maintenance does a CNC probe require?
Regular maintenance is essential to ensure the probe’s continued accuracy and reliability. The specific maintenance schedule may vary depending on the probe type and usage frequency. However, some general maintenance tasks include:
- Cleaning the stylus:Regularly clean the probe stylus to remove dust, debris, and contaminants that could affect its sensitivity.
- Inspecting the stylus:Inspect the stylus for wear or damage that could impact measurement accuracy. Replace the stylus if necessary.
- Checking probe connections:Ensure the probe’s electrical connections are secure and free of corrosion.
- Verifying calibration:Periodically verify the probe’s calibration to maintain measurement accuracy.
- Following manufacturer’s guidelines:Refer to the probe manufacturer’s manual for specific maintenance instructions and recommendations.
4. Is probe for CNC machines expensive?
The cost of CNC probes varies depending on their features, capabilities, and brand. Contact probes are generally more affordable than non-contact probes, which offer higher precision and versatility. However, the investment in a probe can be quickly offset by the gains in productivity, reduced scrap rates, and improved part quality.
When considering the cost of a CNC probe, evaluate the value it brings to your machining operations. Consider factors such as the types of parts you produce, the volume of your production, and the potential cost savings from reduced setup times, improved quality, and minimized scrap.

Katrina
Mechanical Sales Engineer with 10+ years of experience in the manufacturing industry.Skilled in developing and executing sales strategies, building relationships with customers, and closing deals. Proficient in a variety of sales and marketing tools, including CRM software, lead generation tools, and social media. I'm able to work independently and as part of a team to meet sales goals and objectives. Dedicated to continuous improvement and learning new sales techniques.