Email: katrina@qidumetro.com Phone: (+86) 134 1323 8643
Εισαγωγή of Machining Center Probes
Machining center probes are integral to achieving high precision and efficiency in modern machining operations. These sophisticated devices facilitate accurate measurements, ensuring the quality and consistency of machined parts. However, like all mechanical components, machining center probes can face several challenges over time. Understanding these common issues and implementing effective solutions is crucial for maintaining optimal performance and minimizing operational downtime.
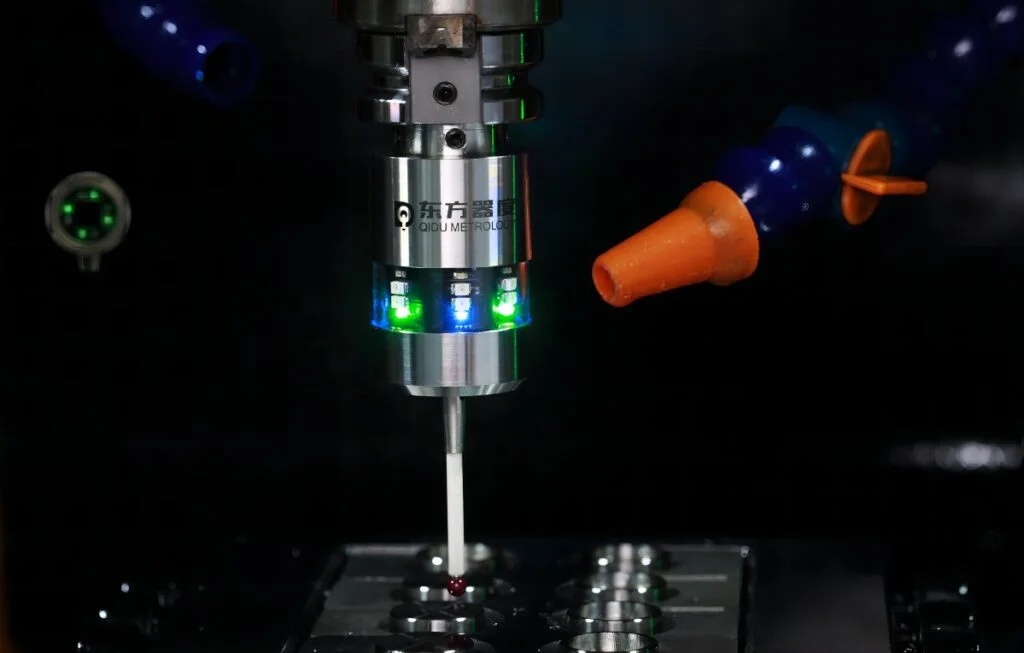
Mechanical Wear and Tear of Machining Center Probes
Over time, machining center probes can suffer from mechanical wear and tear, affecting their accuracy and functionality. The constant use of probes in measuring and positioning tasks can lead to deviations from their original geometry. This wear can result in measurements that are no longer accurate, compromising the quality of the machined parts.
To address mechanical wear and tear, regular maintenance is essential. Establishing a schedule for inspecting probes for signs of wear can help identify issues early. Promptly addressing mechanical problems, such as replacing worn components, ensures the probe continues to operate with high precision.
Electrical Problems of Machining Center Probes
Disruptions from Electrical Issues
Electrical problems, such as faulty connections or power surges, can significantly impact the functionality of machining center probes. These issues can disrupt the probe’s operations, leading to inaccuracies in measurements and potential damage to the probe itself.
Solutions for Electrical Problems
Implementing robust electrical safety measures is crucial to mitigate these issues. Using surge protectors and ensuring proper grounding can prevent power surges from damaging the probes. Regularly checking and maintaining electrical connections also helps in preventing disruptions to the probe’s performance.
Contamination of Machining Center Probes
The Effects of Contamination
Contamination is another common problem for machining center probes. Dust, oil, or debris on the probe’s surface or within the work area can interfere with accurate measurements. Even small particles can affect the probe’s precision, leading to errors in the machining process.
Maintaining a Clean Work Environment
Keeping the probe and its environment clean is key to minimizing contamination. Implementing rigorous cleaning protocols and maintaining a dust-free work zone can significantly reduce the risk of measurement inaccuracies caused by contamination. Regularly cleaning the probe itself ensures it remains free from debris and other contaminants.
Establishing Measurement Routines
Importance of Consistent Measurement Routines
Consistent and well-defined measurement routines are critical for ensuring the reliability of machining center probes. Without a standardized approach, measurement accuracy can vary, leading to inconsistent part quality and potential rework.
Implementing Automated Measurement Routines
Defining specific measurement points and frequencies helps in maintaining the probe’s optimal functionality. Automating these routines can enhance both consistency and efficiency, reducing human error and ensuring accurate data collection across machining operations.
Selecting the Right Machining Center Probe
Choosing the Appropriate Probe for the Task
Different machining applications require different types of probes, each with specific measurement ranges, accuracy levels, and operating characteristics. Selecting the wrong type of probe can lead to suboptimal performance and measurement inaccuracies.
Ensuring Optimal Performance through Proper Selection
Carefully evaluating the requirements of the specific application and choosing a probe that matches these needs is essential. By selecting the appropriate probe, users can ensure they achieve the highest possible performance and measurement accuracy for their operations.
συμπέρασμα of Machining Center Probe
Machining center probes are indispensable tools in the pursuit of precision and efficiency in machining operations. Addressing common issues such as mechanical wear, electrical problems, and contamination, along with establishing consistent measurement routines and selecting the right probes, are crucial steps in maintaining their optimal performance. By implementing these strategies, users can ensure their machining processes deliver consistent, high-quality results, minimizing downtime and enhancing overall productivity.
FAQs: Common Issues and Solutions for Machining Center Probes
1. What are machining center probes, and why are they important?
Machining center probes are precision tools used in machining operations to ensure accurate measurements and positioning. They are crucial for maintaining high-quality and consistent part production.
2. What common issues can affect machining center probes?
Machining center probes can face several issues over time, including:
- Mechanical wear and tear: Leads to deviations in the probe’s geometry, causing inaccurate measurements.
- Electrical problems: Faulty connections or power surges can disrupt probe functionality.
- Contamination: Dust, oil, or debris on the probe or in the work area can interfere with accurate measurements.
3. How does mechanical wear and tear impact probe performance?
Mechanical wear and tear can alter the probe’s geometry, resulting in less accurate measurements and potentially compromised part quality.
4. What steps can be taken to mitigate mechanical wear and tear on probes?
Regular maintenance is key. Implementing a schedule for inspecting and promptly addressing mechanical wear can help maintain the probe’s accuracy and extend its lifespan.
5. How do electrical problems affect machining center probes?
Electrical issues, such as faulty connections or power surges, can disrupt the operation of the probe, leading to inaccurate measurements and possible damage to the probe.
6. What are effective solutions for preventing electrical problems in probes?
Using surge protectors, ensuring proper grounding, and regularly maintaining electrical connections can help prevent disruptions and protect the probe from damage.
7. Why is contamination a problem for machining center probes?
Contaminants like dust and oil can affect the probe’s ability to take accurate measurements, leading to errors in the machining process and compromising part quality.
8. How can contamination be minimized to protect probe accuracy?
Maintaining a clean work environment and regularly cleaning the probe itself can significantly reduce the risk of contamination and ensure accurate measurements.
9. What is the significance of establishing consistent measurement routines for probes?
Consistent measurement routines ensure reliable and accurate data collection, which is crucial for maintaining high part quality and reducing operational variability.
10. How can measurement routines be optimized for better probe performance?
Defining specific measurement points and frequencies, and implementing automated routines can enhance consistency and efficiency, minimizing human error and ensuring accurate data.
11. Why is selecting the right type of probe important?
Different machining applications have varying requirements. Choosing a probe that matches these specific needs ensures optimal performance and accurate measurements.
12. How do you choose the appropriate probe for a specific application?
Evaluate the application’s requirements in terms of measurement range, accuracy, and operating conditions. Select a probe that aligns with these criteria to achieve the best results.
13. What are the key takeaways for maintaining optimal performance of machining center probes?
Understanding and addressing common issues such as mechanical wear, electrical problems, and contamination, along with establishing consistent measurement routines and selecting the right probes, are essential for maintaining optimal probe performance and ensuring consistent, high-quality machining results.

Κατρίνα
Mechanical Sales Engineer with 10+ years of experience in the manufacturing industry.Skilled in developing and executing sales strategies, building relationships with customers, and closing deals. Proficient in a variety of sales and marketing tools, including CRM software, lead generation tools, and social media. I'm able to work independently and as part of a team to meet sales goals and objectives. Dedicated to continuous improvement and learning new sales techniques.