Email: [email protected] Phone: (+86) 134 1323 8643
The relentless pursuit of efficiency is a cornerstone of modern manufacturing. Every step in the production process, from raw material acquisition to final product delivery, is constantly evaluated for potential optimization. In the realm of automated machining, CNC machines play a vital role in achieving high-precision parts with consistent quality. However, a hidden gem within the world of CNC technology exists – the CNC probe tool – and its impact on maximizing efficiency cannot be overstated.
Overview of CNC Probe Tool in Automated Machining
A CNC probe tool is a specialized tool designed to gather data about the position and dimensions of a workpiece within a CNC machine. Unlike traditional machining setups that rely on manual measurements, a probe tool automates the process, seamlessly integrating with the CNC program. This eliminates human error from manual measurements and streamlines the overall workflow.
Importance of Maximizing Efficiency in Manufacturing
Efficiency in manufacturing translates to several key benefits:
- Reduced production costs:Faster setup times, minimized errors, and less rework lead to significant cost savings.
- Increased productivity:By automating tasks and streamlining workflows, CNC probe tools allow for more parts to be produced in less time.
- Improved product quality:Consistent and accurate measurements ensure parts meet stringent quality standards, reducing scrap rates and customer dissatisfaction.
- Enhanced operator safety:Eliminating the need for manual measurements minimizes the risk of operator injury.
Understanding CNC Probe Tool Technology
How CNC Probe Tool Works?
A CNC probe tool functions similarly to a traditional cutting tool but instead employs a sensor at its tip to gather data. This sensor, which can be mechanical, electrical, or optical, transmits real-time information about the workpiece’s location and dimensions to the CNC control unit. The control unit then uses this data to adjust the machining program as needed, ensuring precise tool positioning and pathing.
Benefits of Using CNC Probe Tool in Automated Machining
The benefits of using probe tools in automated machining are numerous:
- Reduced setup times:Automatic tool and workpiece set-up eliminates the need for manual measurements, significantly reducing setup times.
- Minimized errors:Automating measurements eliminates human error, leading to more consistent and accurate results.
- Improved tool life:By detecting tool wear and breakage early on, probe tools help to prevent tool damage and extend tool life.
- Reduced scrap rates:Accurate workpiece positioning and toolpath adjustments minimize the risk of producing out-of-tolerance parts.
- Enhanced in-process inspection:CNC probe tools can be used for in-process inspection, allowing for real-time adjustments and improved quality control.
- Increased process automation:Integration with the CNC program provides a seamless and automated workflow.
Case Studies Showcasing Efficiency Improvements
Several real-world case studies illustrate the efficiency gains achieved with CNC probe tools:
- A manufacturer of aerospace components reported a 40% reduction in setup times and a 25% decrease in scrap rates after implementing CNC probe tools.
- An automotive parts supplier documented a 15% increase in production throughput due to faster tool setup and reduced rework needs with CNC probe technology.
Integration of CNC Probe Tool in Automated Systems
The integration of CNC probe tools with automated systems unlocks even greater efficiency benefits.
Advantages of Integrating CNC Probe Tool in Automated Systems
- Simplified work cell design:Eliminates the need for dedicated fixturing for part alignment, as the probe tool can automatically adjust for variations in workpiece placement.
- Reduced downtime:Automates tasks traditionally performed manually, minimizing machine downtime during setup and changeovers.
- Improved data collection and analysis:Seamless integration with CNC control units allows for real-time data collection and analysis, facilitating continuous improvement initiatives.
Streamlining Processes with CNC Probe Tool
Here’s how probe tools streamline processes in automated systems:
- Automated tool and workpiece setup:The probe tool automatically locates and positions tools and workpieces, eliminating manual intervention.
- In-process inspection:Probes can be used to inspect parts at various stages of machining, ensuring adherence to specifications throughout the process.
- Broken tool detection:Sensors in the probe can detect tool breakage early on, preventing further damage to the workpiece and machine.
- Automatic program adjustments:Based on collected data, the CNC program can be automatically adjusted to compensate for tool wear or slight variations in workpiece dimensions.
Enhancing Accuracy and Productivity
CNC probe tools contribute to enhanced accuracy and productivity in several ways:
- Reduced human error:Automating measurements eliminates operator error, leading to more consistent and precise results.
- Real-time adjustments: The ability to gather data in real-time While probe tools offer inherent efficiency gains, implementing specific optimization techniques can further enhance their impact.
Calibration and Maintenance of CNC Probe Tool
- Regular calibration:Regularly calibrating the probe tool ensures its accuracy and prevents the introduction of errors into the machining process.
- Proper tool cleaning:Maintaining a clean probe tip is essential for accurate data collection. Dust, debris, or coolant buildup can interfere with sensor readings.
- Preventative maintenance:Following the manufacturer’s recommended maintenance schedule helps to identify and address potential issues before they impact performance.
Utilizing Data Analytics for Continuous Improvement
The data collected by CNC probe tools can be a valuable asset for continuous improvement initiatives. Here’s how:
- Identifying process variations:Analyzing probe data can help identify inconsistencies in the machining process, allowing for adjustments to optimize performance.
- Predictive maintenance:By monitoring sensor data over time, potential tool wear or equipment issues can be predicted, enabling proactive maintenance to prevent downtime.
- Process optimization:Data analysis can reveal opportunities to streamline workflows, reduce setup times, and improve overall machining efficiency.
Best Practices for Achieving Maximum Efficiency
Here are some best practices to maximize the efficiency gains from CNC probe tools:
- Invest in operator training:Proper training ensures operators understand how to use and maintain the probe tool effectively.
- Standardize probe tool usage:Develop and implement standardized procedures for using the probe tool across all CNC machines in the shop.
- Utilize offline programming:Take advantage of offline programming software to create and test CNC programs that incorporate probe tool routines.
- Stay updated with technology:Continuously evaluate advancements in CNC probe tool technology and explore opportunities to upgrade for improved capabilities.
Future Trends and Innovations in CNC Probe Tool Technology
The world of CNC probe tools is constantly evolving, with exciting advancements on the horizon.
Emerging Advancements in CNC Probe Tool Technology
- Wireless probe tools:Eliminating the need for wired connections between the probe and the CNC control unit enhances flexibility and simplifies setup.
- On-machine tool verification:Probe technology integrated directly into CNC machines allows for real-time tool verification and adjustments during operation.
- Advanced sensor technology:Developments in sensor technology like laser scanning and vision systems promise even more precise data collection capabilities.
Potential Impact on the Future of Automated Machining
These advancements have the potential to significantly impact the future of automated machining:
- Increased automation:Wireless probe tools and on-machine verification will further automate workflows, reducing manual intervention and human error.
- Enhanced process control:Advanced sensor technology will provide more comprehensive data for real-time process control and optimization.
- Improved flexibility:Wireless connectivity and advanced functionalities will make CNC machining more adaptable to changing production needs.
Importance of Staying Updated with Industry Trends
By staying informed about these trends and actively exploring their potential, manufacturers can position themselves to leverage the next generation of CNC probe tool technology and gain a competitive edge.
Common Questions About CNC Probe Tool in Automated Machining
Here are answers to some of the most frequently asked questions regarding CNC probe tools in automated machining:
1.How does CNC Probe Tool contribute to efficiency?
CNC probe tools contribute to efficiency in several ways:
- Reduced setup times through automatic tool and workpiece setup.
- Minimized errors by eliminating human error from manual measurements.
- Improved tool life by enabling early detection of tool wear and breakage.
- Reduced scrap rates through accurate workpiece positioning and toolpath adjustments.
- Enhanced in-process inspection for real-time quality control.
2. What industries benefit the most from using CNC Probe Tool?
CNC probe tools offer benefits across various industries that rely on precision machining, including:
- Aerospace
- Automotive
- Medical device manufacturing
- Electronics
- Mold and die making
- General machining
3. Are there any limitations to consider when implementing CNC Probe Tool?
While CNC probe tools offer significant advantages, some limitations to consider include:
- Initial investment cost:The upfront cost of acquiring and integrating CNC probe tools may be a barrier for some manufacturers.
- Programming complexity:Implementing probe routines into CNC programs requires additional programming expertise.
- Maintenance requirements:Regular calibration and maintenance are essential for maintaining accuracy.
However, the long-term efficiency gains and improved quality control often outweigh these initial limitations.
In conclusion, CNC probe tools are a powerful technology that can significantly enhance efficiency in automated machining. By understanding their functionality, integrating them effectively into automated systems, and implementing optimization techniques, manufacturers can maximize the benefits of CNC probe tools. As technology continues to evolve, the future of probe tools promises even greater automation, process control, and flexibility for the machining industry.
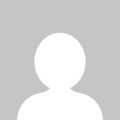
Katrina
Mechanical Sales Engineer with 10+ years of experience in the manufacturing industry.Skilled in developing and executing sales strategies, building relationships with customers, and closing deals. Proficient in a variety of sales and marketing tools, including CRM software, lead generation tools, and social media. I'm able to work independently and as part of a team to meet sales goals and objectives. Dedicated to continuous improvement and learning new sales techniques.