Email: [email protected] Phone: (+86) 158 8966 5308
Tool Setting Arm Series
ARMS FOR CONTACT TOOL SETTER
High motor drive efficiency and good stability
IP68 top-level protection performance
Modular design for easy maintenance
Accurate and reliable measurement results
Integrated over-travel limit to effectively avoid abnormal collisions
Touch Direction | ±X ±Z | |
Positioning Repeatability (6-12” spindle version) | 2σ≤5μm | |
Operating temperature | 5℃-60℃ | |
Storage temperature | -10℃-70℃ | |
Contact force (X Z plane-Machine axes) | 0.75—1.6N | |
Contact force (Y axis-Machine Axis) | 8.0N | |
Trigger force X | XZ plane0.4~0.8N | Y:5.8N |
Protective range | XZ plane+/-12.5° | Y: 6.2mm |
Over travel (X Z plane-Machine axes) | 9.5mm | |
Over travel (Y axis-Machine axes) | 6.2mm | |
Unindirectional repeatability | 2σ≤1μm | |
Protection Rating | IP68 |
Main Function of Tool Setting Arm
- Automatic tool length measurement.
- Automatic monitoring, alarm, and compensation for tool wear or breakage during the machining process.
- Compensation for tool offset changes caused by machine thermal deformation.
- Measurement and compensation of tool offset values in five directions: ±X, ±Z, and Y axes.
Detailed Size for Tool Setting Arm Series
Item No. | Chunk Size (Inch) | Tool Size (mm) | A (mm) | B (mm) |
DMA06 | 6 | 16-20-25-32 | 250 | 219.2 |
DMA08 | 8 | 16-20-25-32 | 286 | 249.2 |
DMA10 | 10 | 16-20-25-32-40 | 335 | 298.2 |
DMA12 | 12 | 16-20-25-32-40-50 | 368 | 298.2 |
DMA15 | 15 | 20-25-32-40-50 | 400 | 343.2 |
DMA18 | 18 | 25-32-40-50 | 469 | 383.2 |
DMA24 | 24 | 25-32-40-50 | 555 | 458.2 |
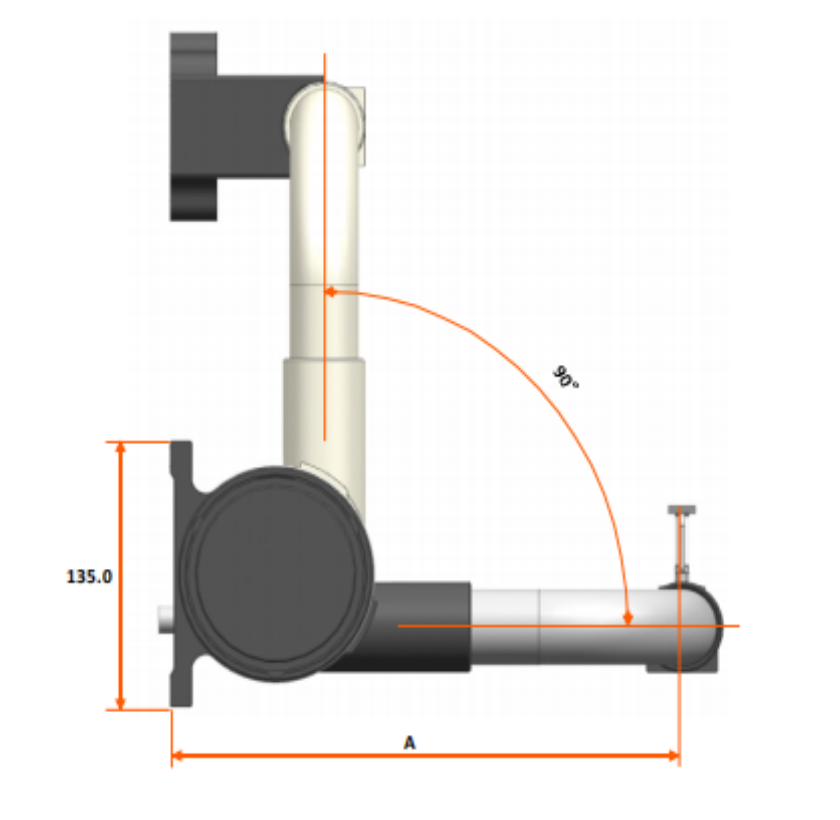



Advantage of Tool Setting Arm
- Save inspection time with the traditional methods
- Reduce errors and minimize scrap
- It offers high precision and reliability in tool offset settings
- Record data automatically, eliminating errors in data entry
- Allows for thermal drift correction through compensation cycles
- Simplify the CNC machine tool system’s call and operation
Breif Introduction of Tool Setting Arm
Qidu’s DMA High-Precision Tool Setting Arm is designed for tool setting and inspection in machining centers, specifically for lathes. It consists of a fixed base and a movable arm, with a touch probe installed on the movable arm. This arm is suitable for various types of spindles or tools.
The tool setting arm and the base are controlled by a torque motor to swing the tool arm out and retract it, introducing a higher level of automation. Importantly, the movement of the tool arm can be programmed into the machining program using M-codes. During the machining cycle, this allows for convenient automated measurement of tool wear, compensation, and monitoring of tool damage. When combined with an automatic loading and unloading mechanism, it enables unmanned machining.


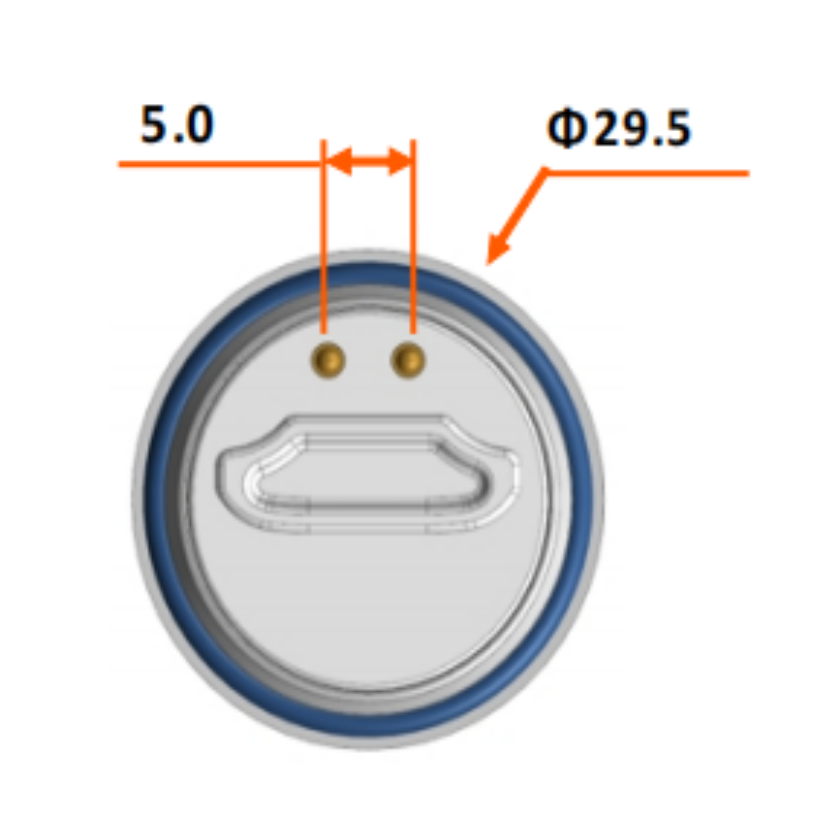
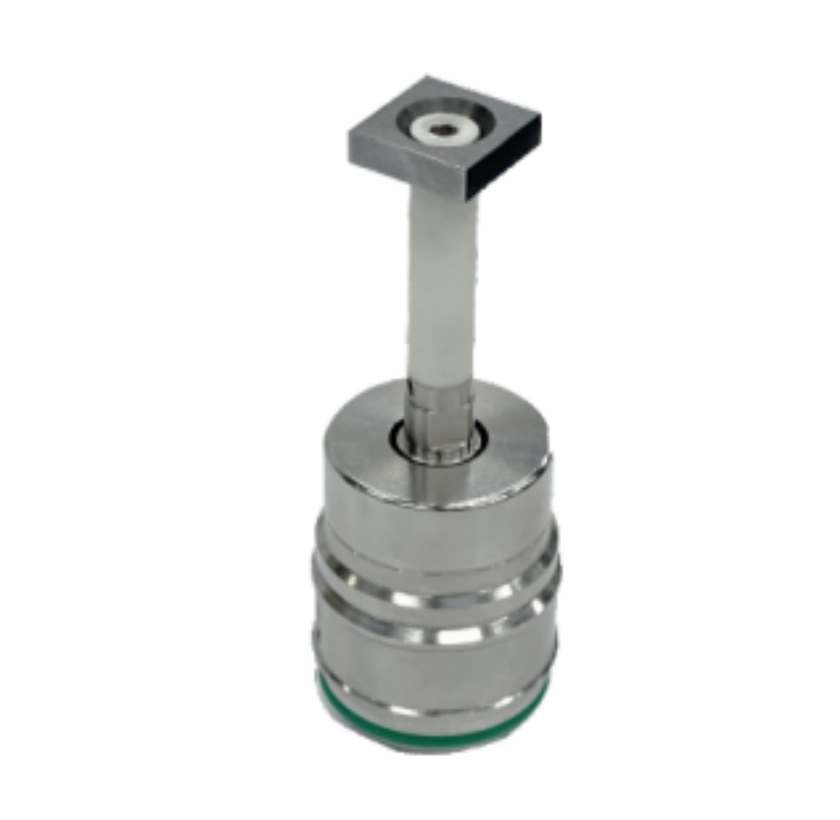
FAQ
Q: What’s the warranty for the product?
We offer one year warranty for the tool.
Q: What’s the function of tool setting arm?
A tool setting arm is a component commonly found in machining and manufacturing equipment, such as CNC machines. Its primary function is to assist in the setup and calibration of cutting tools used in machining processes. Here are some key functions of a tool setting arm:
1. Tool Length Measurement: The tool is used to measure the length of cutting tools accurately. This information is crucial for the CNC machine to precisely position the tool during machining operations.
2. Tool Diameter Measurement: In addition to tool length, the tool can also measure the diameter of the cutting tool. This data helps in determining the correct offsets and adjustments for the machining program.
3. Tool Wear Compensation: Over time, cutting tools can experience wear, affecting the accuracy of machining operations. The tool setting arm allows for the measurement of tool wear, enabling the CNC machine to compensate by adjusting tool offsets for continued precision.
4. Tool Offset Calibration: The tool helps in calibrating the tool offsets accurately. Tool offsets are necessary to compensate for variations in tool dimensions, ensuring that the machined part matches the programmed design.
5. Automatic Tool Changes: CNC machines often have multiple tool stations, and the tool setting arm facilitates automatic tool changes. It helps in quickly and accurately positioning and measuring each tool during the tool change process.
6. Reducing Setup Time: By automating tool measurement and calibration processes, the tool setting arm contributes to reducing setup time. This is particularly important in environments where frequent tool changes and adjustments are required.
Q: What kind of machine is available for the tool setting arm?
The tool is available for the following machines: CNC Machining Centers, Coordinate Measuring Machines (CMM) ,Tool Presetter, Grinding Machines, Multi-Function Machines and so on.