Email: katrina@qidumetro.com Phone: (+86) 134 1323 8643
Functions of Qidu Metrology Tool Setter
- Tool Measurement
- Tool Offset Calculation
- Tool Length Calibration
- Tool Diameter Calibration
- Tool Wear Compensation
- Tool Inspection
- Tool Presetting
- Tool Breakage Detection
- Tool Condition Monitoring
- Tool Error Detection
CNC Lathe Tool Setter
Qidu Metrology CNC Machine Tool Setter, a cutting-edge device designed to enhance precision and efficiency in machining operations. This indispensable tool serves as a crucial component in the setup and calibration of CNC machines, ensuring accuracy in tool length measurements.
Our Tool Height Setter boasts advanced features, including high-resolution measurement capabilities and user-friendly interfaces. With its state-of-the-art technology, it streamlines the tool-setting process, saving valuable time and reducing the likelihood of errors during machining.
Key highlights of our CNC Machine Tool Length Setter:
- Precision Measurement: Achieve unparalleled accuracy in tool length measurement for precise machining results.
- User-Friendly Interface: Intuitive controls make it easy to operate, reducing the learning curve for operators.
- Time Efficiency: Streamline setup procedures, optimizing workflow and enhancing overall productivity.
- Compatibility: Designed to seamlessly integrate with a variety of CNC machines, ensuring versatility in application.
Investing in our CNC Machine Tool Length Setter means investing in the future of your machining operations. Experience heightened precision, increased efficiency, and seamless integration into your existing workflow. Elevate your machining capabilities with our cutting-edge tool length setter.
Why Customers Choose Qidu Metrology Tool Setter
- Precision: Unmatched accuracy for precise measurements.
- Durability: Long-lasting quality for consistent performance.
- Efficiency: Streamlined processes for faster production cycles.
- Versatility: Adaptable for various machining applications.
- Ease of Use: Intuitive interface for user-friendly operation.
- Reliability: Consistent results ensure dependable performance.
- Cost-effectiveness: Value-driven solution for budget-conscious buyers.
- Support: Dedicated customer service for ongoing assistance.
Tool Setter Type
The Advantages of Using A Tool Height Setter:
- Reducing CNC machine downtime and enhancing its dependability
- Mitigating the production of faulty items due to tool breakage
- Ensuring precise measurements of tool length and diameter, along with accurate tool offset calculation and adjustment
- Offering exceptional accuracy, stability, and a repeatability rate of 0.001mm
- Providing a warranty period of 1 year, with readily available spare parts, and prompt resolution of any issues by our dedicated after-sales team
- Offering competitive pricing, presenting a cost-effective alternative compared to leading brands such as Blum, Marposs, and Metrol.
- Streamlining workflow processes and increasing overall productivity
- Enhancing operator efficiency through simplified tool setup procedures
- Facilitating proactive maintenance scheduling, thereby extending equipment lifespan
- Enabling seamless integration with existing CNC systems for improved operational synergy.

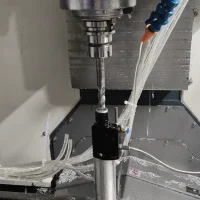
FAQ of Tool Setter
Q: What is a tool setter?
A tool setter is a device used in manufacturing and machining processes to set and measure the dimensions of cutting tools or workpieces. It plays a crucial role in ensuring precision and accuracy in machining operations. The tool setter is typically used with machine tools such as CNC machines, milling machines, and lathes.
Q: Is the role of a tool setter crucial in CNC machining?
Yes, it is crucial in CNC machining. A tool setter is responsible for setting up and maintaining the cutting tools used in CNC machines. This includes installing, adjusting, and ensuring the proper alignment of cutting tools in the machine.
Q: How do you use a tool setter?
Here’s a general guide on how to use a tool setter:
- Mounting the product.
- Initialize the CNC Machine.
- Load the Tool.
- Position the Tool Setter.
- Bring the Tool Close to the Setter.
- Touch-Off Procedure.
- Record the Offset or Length.
- Calculate Offset Values.
- Enter Offset Values into CNC Program.
- Verification.
- Repeat for Each Tool.
Q: What is the tool setting process?
The tool setting process involves configuring and calibrating tools for optimal performance in various applications. It includes adjusting parameters such as tool geometry, cutting speeds, and feed rates to ensure precision and efficiency in machining or other processes. Proper tool setting enhances overall productivity and quality.
Email: Katrina@cnctouchprobe.com
Phone:(+86) 134 1323 8643